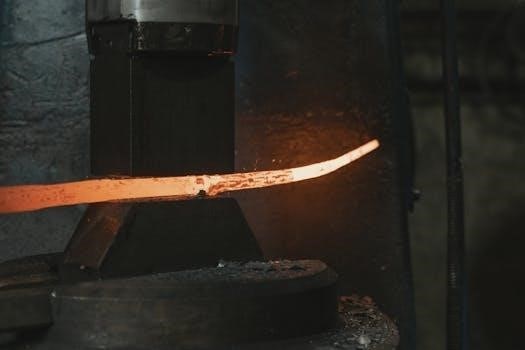
The 5 in 1 combo heat press machines are versatile tools for hobbyists and professionals, providing fast and even heating․ They transfer designs onto various flat and curved objects, handling t-shirts, bags, hats, mugs, plates, and more with ease․
Overview of Multi-Functionality
These 5-in-1 combo heat press machines are designed with versatility in mind, combining several functions into one convenient device․ They are not just limited to t-shirts; their multi-functionality extends to a wide array of items․ This includes, but is not limited to, pressing designs onto mugs, plates, hats, and even shoes, making them a comprehensive solution for various crafting and customization needs․ The ability to switch between different attachments easily makes them incredibly adaptable for various projects․ These machines often include a flat platen for fabrics, as well as curved attachments for items such as mugs and hats․ The user can quickly change between these attachments without the need for multiple machines․ This makes the 5-in-1 heat press an ideal tool for small businesses or hobbyists who need a diverse range of capabilities within a single unit, streamlining the production process and saving space․
Key Features of 5 in 1 Combo Heat Presses
Key features include advanced heating technology, a user-friendly control panel, and interchangeable attachments․ These machines offer a large working area, ensuring efficient and precise heat transfer for various projects․
Heating Technology and Performance
The heating technology in 5-in-1 combo heat presses often utilizes a double-tube system for uniform heat distribution across the platen․ This ensures consistent transfer results on various materials․ The machines typically feature aluminum platens coated with temperature-resistant materials for safe handling․ The heating elements are designed to reach high temperatures, often up to 570°F, with precise temperature control for different transfer needs․ Many models incorporate a rapid heating process, minimizing waiting time and maximizing productivity․ The performance is further enhanced by reliable motherboards and accurate temperature control devices, contributing to the stability of the heat transfer․ These features collectively ensure that the heat press delivers consistent and high-quality results, whether working with fabrics, ceramics, or other materials, making it a versatile tool for any project․ The heating system is also designed to be efficient, reducing energy consumption while maintaining optimal performance․
Control Panel and User Interface
The control panels of 5-in-1 combo heat presses are designed for intuitive operation, typically featuring an LCD display for clear visibility of settings․ Users can easily set the temperature and time using simple button controls․ The interface often includes indicators for heating status and timer functions, allowing for precise control over the heat transfer process․ The user interface is designed to be user-friendly, even for beginners․ Some models include preset settings for various materials, making the setup process faster and easier․ Digital controls ensure accurate adjustments, which is essential for consistent results․ The intuitive design of the control panel minimizes the learning curve, enabling users to start creating their designs quickly․ The feedback provided through the interface ensures that users can easily monitor the progress of their heat transfer projects, leading to successful outcomes․ The controls are also usually robust and built to last․
Operational Guidelines
Operating a 5-in-1 heat press requires careful attention to detail․ Setting the correct temperature and time is crucial for successful transfers․ Always follow safety precautions to avoid accidents and ensure a safe working environment during operation․
Setting Temperature and Time
To set the temperature on your 5-in-1 heat press, use the control panel, often an LCD screen, to input the desired temperature, typically in Fahrenheit․ The heating range can go up to 570°F, but specific materials will have their own recommended settings․ Use the plus or minus keys to adjust the temperature, and always double check for accuracy․ For the time setting, press the designated setup button to switch to the time function․ Then, using the same plus or minus keys, input the required time, usually in seconds, with a range up to 999 seconds․ Each material will require a specific time․ After setting both temperature and time press the setup button again to save settings and prepare to start working․ Remember to consult a material guide for the optimum heat and time settings for each project to achieve the best results․
Safety Precautions During Use
When operating a 5-in-1 combo heat press, always prioritize safety․ Ensure the machine is placed on a stable, heat-resistant surface․ Always switch off the machine and unplug the power cord when not in use․ The heat platen will cool to room temperature after about 30 minutes of inactivity․ Be aware that the heat-releasing fan will start automatically when the platen reaches 176°F (80°C)․ Never leave the machine unattended while it’s heating․ Avoid touching the hot platen directly, and use heat-resistant gloves when handling hot items․ Keep children and pets away from the operating area․ Make sure the area is well-ventilated to prevent overheating․ Never attempt to repair the machine yourself; contact a professional if issues arise․ Inspect the power cord for damage before each use․ Ensure that your outlet is not overloaded to prevent electrical issues․ Always be mindful of potential electrical surges․
Troubleshooting Common Issues
Users may encounter problems like uneven pressure or temperature deviations․ Other issues include poor transfer effects, not counting down, or the machine not turning on․ Knowing how to address these is crucial․
Problems with Heating and Power
If your heat press isn’t heating, a faulty heat sensor could be the culprit; they can burn out due to excessive heat․ The relay switch, which controls power flow, might also be defective, or have loose connections preventing heating․ Loose platen connections, often from wire soldering coming off due to heat, can also cause this issue․ Insufficient power from the outlet might also be the problem, especially if the machine isn’t receiving its required wattage․ If the machine won’t turn on at all, check for a damaged power cable, often caused by high heat or inconsistent power․ A blown fuse, which acts as a mini-breaker, could be the reason․ Look for blackening on the ends of the fuse․ Inspect the circuit board for damage or loose connections․ Finally, a faulty breaker, compromised wires, or an overloaded outlet can cause the machine to shut off suddenly․ Overheating, due to a malfunctioning temperature system or damaged elements, can also trigger the breaker․
Issues with Print Quality and Transfer
Poor print transfer can often be attributed to insufficient heat or pressure during the process․ Always verify that the material you’re using is compatible with heat transfer vinyl, and if it has a water-repellent or antimicrobial coating it is often unsuitable․ Each vinyl type has unique temperature, time, and pressure needs; always refer to the manufacturer’s instructions․ Overheating can scorch fabrics so always check the material’s optimum temperature and test on a spare piece․ Uneven placement or a crooked design can result from not pre-pressing the fabric or not positioning it correctly․ Color transfer issues may arise from prolonged heat exposure or if the material is low-quality․ Avoid over-pressing and ensure you use high-quality material․ If the design does not adhere correctly, check the pressure and temperature settings again and consider that a faulty heating element may be to blame․
Addressing Temperature Fluctuations
Temperature fluctuations are a common issue, often stemming from a compromised temperature system․ Overuse, excessive heating, and inadequate ventilation can damage the system, causing the temperature to drop below the set point․ Insufficient power supply can also affect heating elements, leading to inconsistent temperatures․ If your heat press keeps dropping below the set point, the temperature system is likely broken․ Contact the supplier or manufacturer for replacement of compromised components․ It’s not unusual for new heat presses to have temperature settings off by 18 to 20 degrees․ To calibrate this, set the temperature to 380F on the control panel, wait for it to reach the temperature, and then use a thermometer to check the actual temperature․ Adjust the temperature settings based on the thermometer readings․ Remember, the heat-releasing fan should automatically start when the heat platen reaches 176 degree F․
Leave a Reply
You must be logged in to post a comment.